Kickmaker est une communauté d’ingénieurs et d’experts métiers en industrialisation, que de plus en plus d’entreprises – et de designers – utilisent pour la conception et la réalisation de pré-séries de produits.
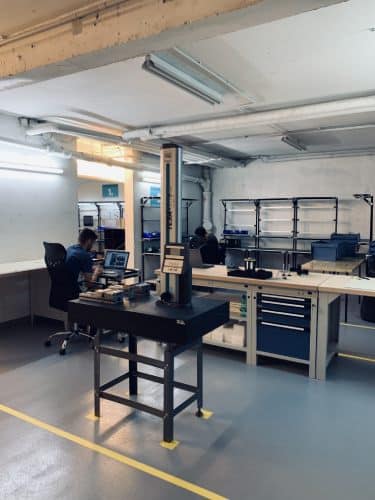
Kickmaker accompagne start-up, PME et grands groupes dans l’industrialisation de leurs produits, du prototype au mass-manufacturing. La société, créée en 2016 par Eric Elmlas, ancien directeur de l’industrialisation chez Aldebaran (à l’origine des robots humanoïdes Nao et Pepper) et Vincent Despatin, ancien responsable des opérations d’Altran en Chine, évolue dans les domaines des drones, de la robotique, des machines médicales, des machines spéciales, des nouvelles mobilités ainsi que des objets connectés. Implantée sur trois sites – Paris, Lyon et Shenzhen – Kickmaker a bouclé fin 2019 une levée de fonds de cinq millions d’euros qui permettra d’amplifier à la fois recrutement et expan-sion géographique. “Nous avons lancé en juin 2019 un concept de micro-usine consacrée à la pré-série de produits high-tech à Paris et Lyon et nous ouvrirons prochainement une micro-usine plus vaste dans le 15e arrondissement de Paris” indique Alysée Flaut, la responsable de la communication de Kickmaker. Avec 130 collaborateurs, Kickmaker est le seul acteur français à détenir la capacité à réali-ser des pré-séries en France dans une adéquation coût-qualité-délai attractive.
“Le design pratiqué chez Kickmaker est une activité de conception, selon l’acception anglo-saxonne du terme. Le but est de déterminer la structure ho-mogène d’un produit afin de résoudre l’ensemble des contraintes industrielles qui s’y rattachent, en tenant compte des contraintes techniques, économiques, ergonomiques et fonctionnelles. Nous pensons l’objet en intégrant systématiquement les contraintes économiques et de production” précise Alysée Flaut qui ajoute que “même si nous disposons d’un designer dans nos équipes – Vincent Le Roux, qui est également ingénieur mécanique – nous ne faisons pas de design industriel à proprement parlé mais travaillons en étroite collaboration avec des agences de design extérieures comme, par exemple, Elium ou OVA Design. Il peut néanmoins arriver que nous soyons, à certaines occasions, force de proposition en matière de design”.
En réalité, Kickmaker s’appuie sur une démarche de création tripartite : “dans la plupart des cas, le client consulte d’abord une agence de design avant de contacter des partenaires industriels. Nous intervenons donc le plus souvent en second point de contact”, indique Alysée Flaut qui précise d’autre part que “les designers définissent l’apparence extérieure, les premières fonctionnalités et nous fournissent les premiers dessins, ou les fichiers 3D des surfaces extérieures. C’est alors que nous prenons connaissance de leurs propositions et les étudions, déterminons ce qui est faisable ou non en fonction des possibilités techniques, de l’adéquation avec les fonctionnalités attendues, des contraintes budgétaires, puis envoyons à notre tour nos commentaires. Les designers font de nouvelles propositions, le client en sélectionne une et nous travaillons pour en faire un modèle industrialisable. Puis, nous invitons les équipes mécaniques, électroniques, mécatronique à plancher sur le sujet. Nous formalisons les concepts design par des modélisations 3D qui permettent d’obtenir des représentations en perspective des produits et d’en décrire les usages. Nous réfléchissons au choix des matériaux en fonction des contraintes techniques, à la gestion des grands assemblages, au processus d’industria-lisation, à la maîtrise des coûts de production ainsi que du coût de revient, et aux partenaires industriels futurs qui seront en mesure de produire l’objet. En tant qu’industriel, nous corrélons la dimension esthétique et pratique avec la fabricabilité du produit”. Pour Alysée Flaut “notre rôle premier est d’accom-pagner les agences de design dans la maturation de leur produit”. Elle précise que deux cas de figures existent : “certaines agences de design sont trop éloignées des problématiques et contraintes industrielles dans leur démarche de création produit. Elles imaginent des produit difficilement conce-vables industriellement. Dans ce cas, nous reprenons la main sur le design. Au contraire, d’autres agences réalisent un travail poussé, par exemple sur la résistance structurelle, l’assemblage, les interfaces homme/machine et facilitent par la suite les échanges entre les différents protagonistes (eux, nous et le client). De façon générale, les agences de design orientées design industrie qui travaillent déjà avec des bureaux d’étude ont une meilleure com-préhension des contraintes industrielles et notamment des compatibilités géométriques avec les matériaux. Elles fournissent un travail préliminaire plus poussé, qui prend en compte les problématiques de production”.
Kickmaker envisage son rôle vis-à-vis du design de façon très pragmatique : “nous concevons, architecturons, développons et évaluons des systèmes mécaniques innovants en intégrant les différentes expertises métiers, en particulier celles de l’ergonome et du designer industriel dans les projets. Au lieu d’approcher le produit final par l’esthétique, nous l’approchons plutôt par la fonction. Nos connaissances sur les propriétés des matériaux, l’injection plastique et autres processus industriels et techniques sont essentielles, notamment dans les principes d’emboîtements, de pliage ou de fixation des éléments”. Kickmaker dispose dans ses micro-usines – dénommées KAL pour Kickmaker Assembly Line – du savoir-faire et des moyens permettant de commencer à tester une conception via des imprimantes 3D, d’en étudier les propriétés mécaniques (clips, fûts de vis, emboîtements) ou d’évaluer un rendu es-thétique selon les matériaux, comme passer du plastique traditionnel au bio-sourcé. La KAL “est idéale pour fournir des produits semi finis en petite série ou des produits finis fonctionnels avec les matériaux définitifs, pour réaliser les gammes d’assemblage, les set-up de lignes d’assemblage ou encore les tests de pré-certification” indique Alysée Flaut.
Un article de Christophe Chaptal
Article précédemment paru dans le Design fax 1143