De la production locale de maquettes à la fabrication de pièces en titane pour l’aéronautique et la création de nouvelles œuvres d’art, l’impression 3D se déploie tous azimuts. Le détail avec Christophe Chedal Anglay, Stéphane Simon et Catherine Gorgé de Prodways, leader du secteur.
Directeur du design de Petzl, le spécialiste des équipements pour la montagne, et designer de yachts, Christophe Chedal Anglay sculpte depuis longtemps avec un logiciel 3D. Après un travail décevant avec un opérateur, il prend en main la souris, apprend à se servir des logiciels pour pouvoir maîtriser de bout en bout ses réalisations. Dès 1996, il réalise des maquettes numériques qu’il peaufine avec des prototypes en stéréolithographie. L’avantage ? “Le designer veut que ce qu’il designe arrive sur le marché, explique le natif de Courchevel et désormais Annécien. La stéréolithographie permet de vérifier rapidement la fiabilité de la proposition. Il n’y a aucune perte en ligne entre l’idée et sa réalisation finale.” C’est aussi le meilleur moyen de communiquer avec le client : il peut tenir l’objet en main, le sentir, en comprendre l’ergonomie. Une maquette est plus démonstrative qu’une image numérique. Le prototypage, pourtant, est loin d’être le seul champ d’action de l’impression 3D. Depuis 2010 et grâce à l’amélioration des processus, elle est devenue un véritable outil de production industrielle.
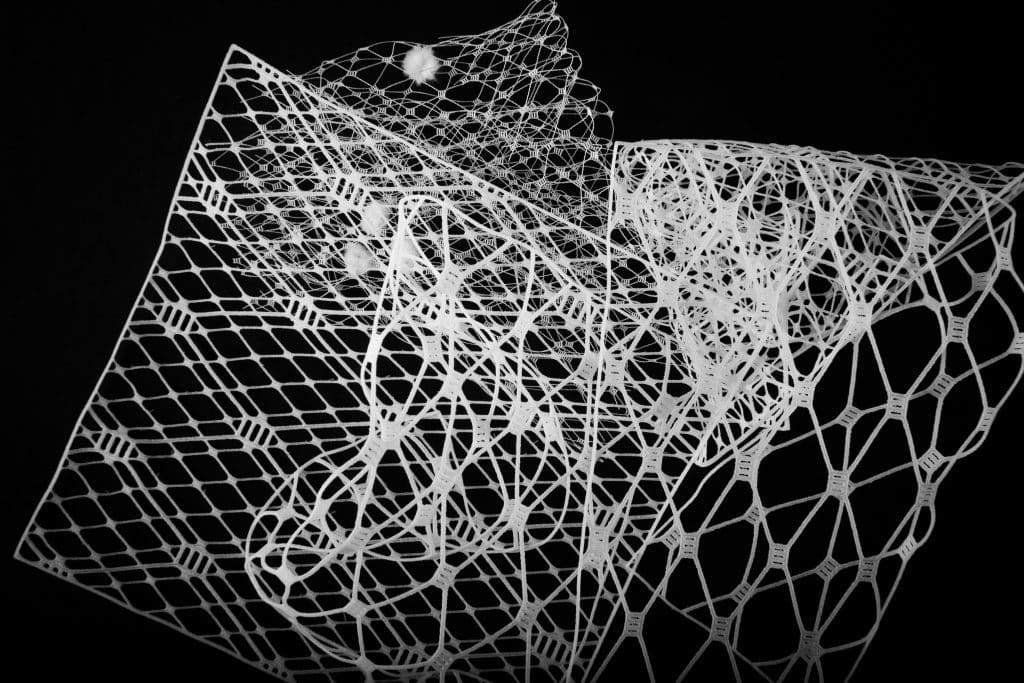
“Elle permet de réaliser des petites séries comme pour les platines d’adaptation pour poser les lampes frontales Petzl, poursuit le designer. Grâce au développement des techniques, à la diffusion des machines, elle autorise une massification de la personnalisation.”
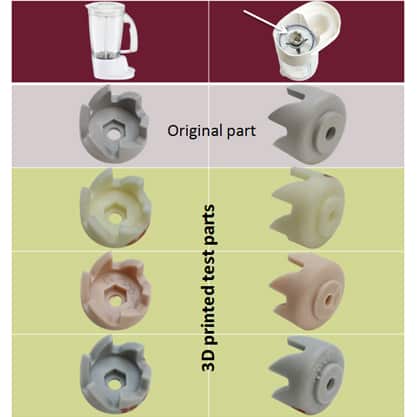
Plus besoin de rentabiliser par un prix élevé ou une production de masse les moules coûteux et long à fabriquer, ceux-ci disparaissent au profit d’une forme dématérialisée et modifiable à l’infini: le fichier numérique 3D. Soit un gain de temps, la possibilité de produire à la demande, et localement. Plus besoin de stocks, l’impression relativement rapide de petites pièces permet même de prolonger la vie des produits de consommation courante. Le fabricant d’électroménager Seb teste ainsi depuis un an l’impression de pièces de rechange alors que le distributeur Boulanger a lancé Happy3D, une plateforme permettant de télécharger des fichiers de pièces détachées à imprimer. Écologique ou développement durable, la 3D ? Une méthode prisée par le designer Patrick Jouin qui y voit aussi un des moyens de produire de manière frugale à l’heure de la raréfaction des ressources. Par son principe “additif” – agglomération ou dépôt de couches successives de matière- la technologie ne produit que très peu de déchets.
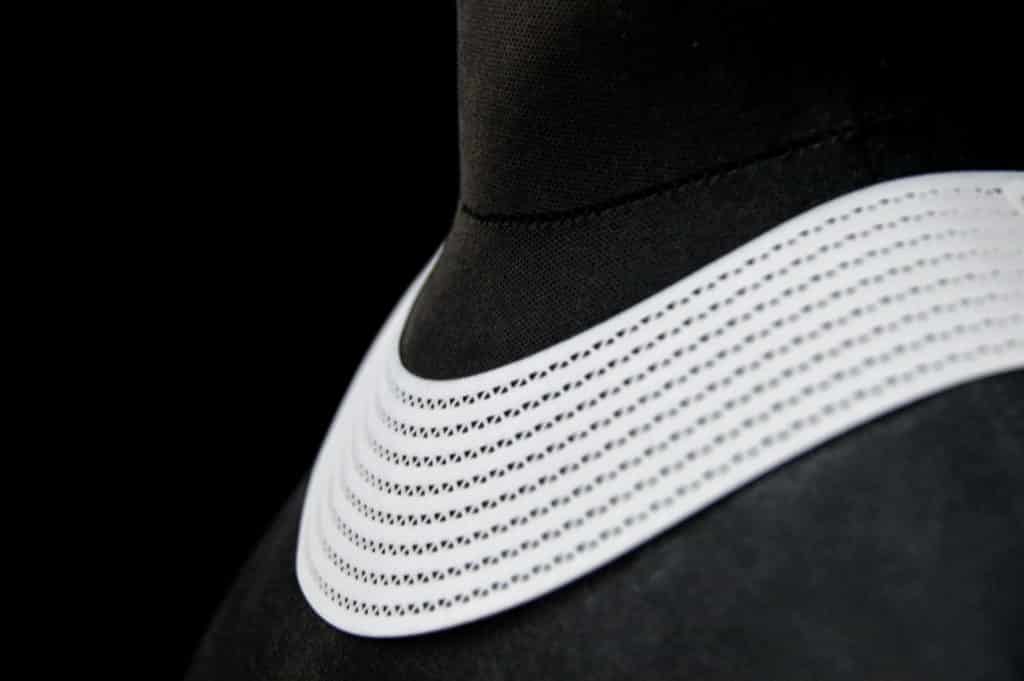
Explorée depuis une trentaine d’année l’impression plastique reste majoritaire. Elle représente 71% de la matière imprimée et est proposée par 51% des services d’impression d’après le rapport 2017 du cabinet de consultants Wohlers. Mais les différentes compositions se multiplient. Le TPU, par exemple, un élastomère, permet d’imprimer des matières souples avec des applications possibles dans la mode et le luxe. Ce polyuréthane thermoplastique permet ainsi au Français Prodways de produire des semelles pour Nike comme des cols pour de grandes marques de luxe.
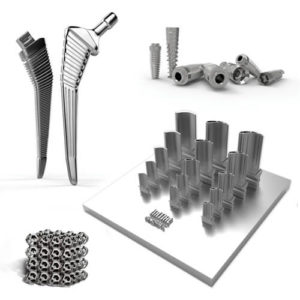
Le métal représente déjà 11% du marché et devrait continuer à croître. “La solidité des pièces de titane, est équivalente à celle des pièces manufacturées ou même meilleure, souligne Christophe Chedal-Anglay. Et elles sont beaucoup plus légères, ce qui est important pour les bateaux de courses.” Grâce à l’optimisation topologique des pièces autrefois usinées peuvent être affinées sans perdre de leur résistance et en permettre de réaliser des économies d’énergie. L’Airbus A 350 XWB vole déjà avec plus de 1000 pièces imprimées, ce qui lui permet de consommer 25% de carburant en moins que ses concurrents (denier rapport EY). Les chiffres de General Electric, le géant de l’impression 3D sont aussi parlants : la fabrication en impression 3D d’un injecteur-carburateur en métal a ainsi permis de réduire le poids du moteur de 25% tout en offrant une résistance cinq fois supérieure à celle des injecteurs fabriqués de manière conventionnelle. Avec des gains de productivité considérables (jusqu’à 30%) et une réduction de la consommation de carburant CO2 de 15% par rapport aux moteurs actuels.
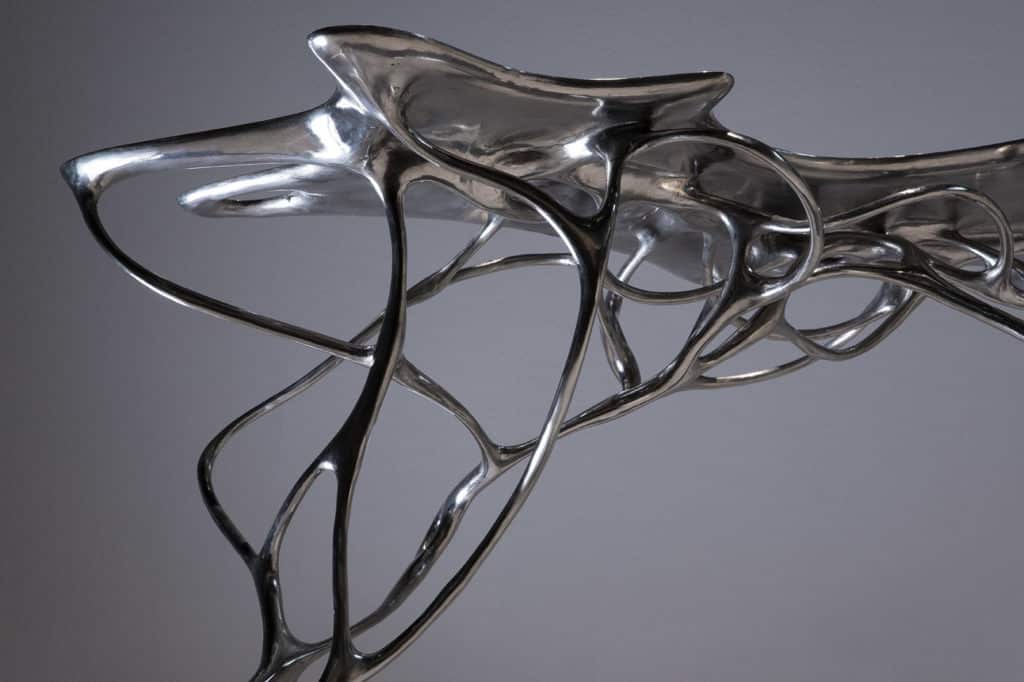
En France, le leader Prodways, compte bien s’installer à la troisième place mondiale d’un secteur toujours plus concurrentiel. Sa croissance économique est aussi rapide que les technologies qu’il développe : 18% de hausse du chiffre d’affaires au premier semestre 2017 par rapport à 2016. La force de l’entreprise du groupe Gorgé comparé à un Sculpteo ? Elle est présente sur l’ensemble de l’écosystème, de la conception et la fabrication des machines jusqu’à la production de pièces en 3D en passant par l’élaboration des matières à imprimer comme du développement des logiciels. Si elle réalise d’abord des pièces pour l’industrie médicale ou aéronautique, elle développe depuis un peu plus d’un an son offre à l’attention des designers, des architectes et du monde de l’art avec sa filiale Initial, à Annecy et rachetée en 2015. Objectif ? Devenir le numéro un mondial du domaine.
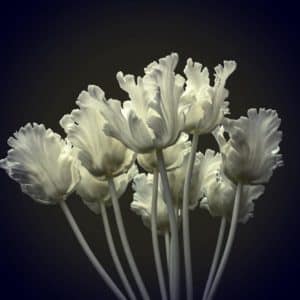
“Nous fabriquons à la demande des pièces uniques ou des petites séries, détaille Catherine Gorgé, secrétaire générale de Prodways et directrice de la division luxe “Les créations”. Plus d’un million sont sorties l’année dernière contre 500 000 au moment du rachat.” Avec 70 ingénieurs qui accompagnent les projets, 30 machines qui peuvent tourner 24h sur 24 – 20 imprimantes plastiques, 10 métallique-, l’usine produit aussi bien de minuscules moules de fonderie à cire perdu pour des bijoux que des très grands formats en plastique ou en métal. “Nous sommes la main du designer, poursuit l’ancienne élève de centrale Marseille passée par la pétrochimie avant de travailler pour la marque Paco Rabanne chez Puig et de rejoindre le groupe Gorgé dirigé par son mari. Nous apportons savoir-faire et valeur ajoutée. La 3D permet d’ouvrir le champ des possibles, de réaliser des formes complexes qui ne pouvaient l’être avant.” Comme la table en titane de Mathias Bengtsson montrée au Centre Pompidou pendant l’exposition Imprimer le monde. Elle a nécessité 310 heures de fabrications, – impression de la dizaine de blocs nécessaires, assemblage soudure et polissage manuel (photo de une). Si la technologie offre de plus en plus de précision, elle n’oblitère pas (pour l’instant ?) la manutention et le travail humain, que ce soit pour les opérations sur écran et avec les logiciels ou plus traditionnellement pour les finitions. Créée par des ingénieurs venus du fabricant de ski Salomon, l’entreprise s’y connait en surfaces lisses…
La 3D a besoin de l’homme pour atteindre la perfection. “Il a fallu 200 heures de limage, ponçage etc. pour atteindre la perfection que je recherchais,” assure Stéphane Simon qui a réalisé les pièces de son installation In memory of me avec le Savoyard. Pour la beauté d’un geste entr’aperçu à Barcelone, celui d’un homme en train de se prendre en photo avec un téléphone portable, le designer et plasticien a voulu le reproduire, le singulariser, l’interroger sous la forme d’une installation sous-titrée Vers un nouveau catalogue de geste. “Enlevez le téléphone, relève Stéphane Simon, et il reste une forme d’élégance, de plasticité à la fois toute nouvelle dans l’histoire du mouvement et très ancienne puisqu’elle rappelle la statuaire grecque. Comme elle, le selfie a pour objet de promouvoir, de glorifier.” A l’élite antique des hommes sculptés s’est substituée la foule contemporaine des hommes qui se photographient : Google a compté 24 milliards d’autoportraits en un an sur ses “seulement” 200 millions de compte Google photos. La passion est commune, mais le geste lui-même est-il vraiment vu ? Le designer le présente dans toute sa nudité avec quatre statues de quatre postures différentes.
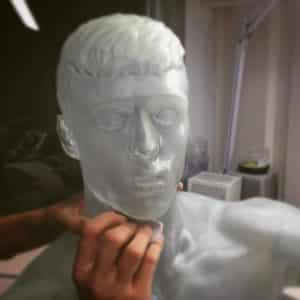
A geste contemporain, technique contemporaine (on ne sculpte plus rien dans le marbre) : l’impression 3D donc, qui est la seule à permettre une reproduction idéale. “Il y a quelques années à peine, la qualité que je cherchais n’était pas au rendez-vous, remarque celui qui est aussi directeur général du Lieu du design. Les progrès son rapide.” Après une longue quête pour trouver le modèle qui lui sied, un mannequin aux proportions les plus parfaites possibles, Stéphane Simon déniche Andres Sanjuan Villanueva. Le jeune homme a ensuite été scanné nu par une centaine d’appareils photos afin de réaliser un fichier numérique le plus détaillé possible. Quinze jours de nettoyage de l’image 3D et de retouches (sauf pour le visage) seront nécessaire pour que la représentation du jeune homme épouse les canons grecs (la hauteur du corps égale huit fois celle de la tête) avant de lancer l’impression. Chaque sculpture grandeur nature, 1m80, a été imprimée en dix morceaux par stéréolithographie. Puis l’ensemble en résine a été emboîté, limé, poncé… Chaque statue pèse 10kg avec sa peau de 3 à 4 cm d’épaisseur qui entoure du vide. Une mise en abyme du selfie masquant sa vanité sous une apparence de vérité “photoshopée” et reproductible à l’infini ?
La question de la copie est de celles qui passionnent Catherine Gorgé. Elle a été contactée par la Société des auteurs dans les arts graphiques et plastiques (ADAGP) pour travailler à une charte éthique concernant la reproduction. “Comment savoir que l’on a affaire à une copie quand on peut scanner une œuvre puis la reproduire à l’infini à partir d’un seul fichier ?,” s’interroge la dirigeante.